Products
Maxblend Reactor

Excellent agitation characteristics for various types of mixing: liquid-liquid, solid-liquid, gas-liquid
Overview
The multi-functional "Glass Lining Maxblend Reactor" is a product realized by fusion of NGK Chemitech glass lining technology and Sumitomo Heavy Industries Process Equipment agitation technology.
We have added the results of our latest research and development to the technology and abundant experience We offer a variety of solutions that are based on our long experience in the industry and cutting edge studies.
Go to Sumitomo Heavy Industries Process Equipment Co.,Ltd. home page.
Caution
This product is among the restricted product types listed in Appended Table 1 of the Japanese Export Trade Control Order.
Export requires export permission from the Japanese relevant governmental authority based on the Foreign Exchange and Foreign Trade Act and other relevant laws of Japan.
Product highlights
- Complete mixing in a short time
- Compatible with a wide range of viscosities
- Stable to changes in liquid level
- Excellent heat transfer characteristics
- Low power consumption
- Uniform solid dispersion
- Easy particle size control
- Minimum adhesion
- Good aeration and agitation characteristics
- Excellent corrosion resistance by Glass lining
Features
1. Complete mixing in a short time
An innovative flow pattern enables uniform mixing in a short time.
Agitation power (Pv) vs. Time for complete mixing (θM)
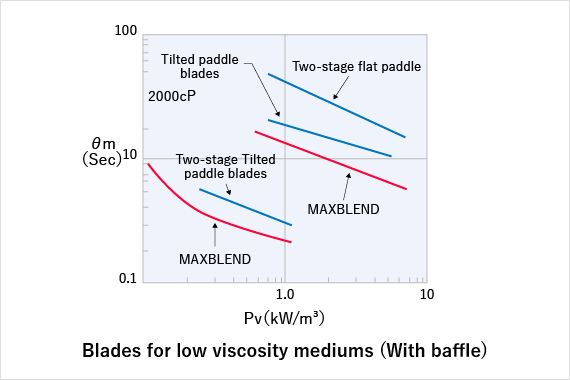
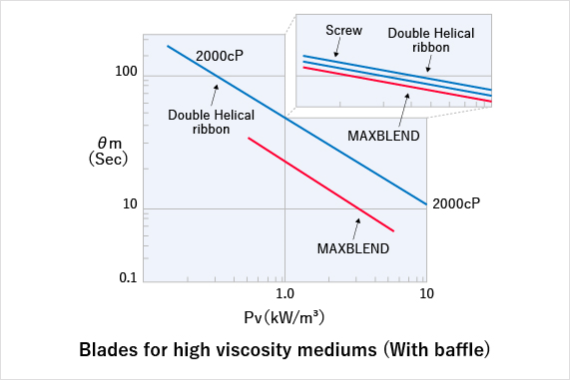
Mixing time comparison
![Mixing of the Maxblend. Mixing of the double helical ribbon blade. MAXBLEND [Viscosity: 20,000cp Rotation:115rpm Unit force: 2.0kW/m³] MAXBLEND [Viscosity: 20,000cp Rotation:43rpm Unit force: 2.0kW/m³]](/en/resource/img/product/glass-lining/maxblend/product-pic04.png)
2. Supports a wide range of viscosities
Compared to conventional blades, this product demonstrates stable mixing performance in a wide range of viscosities from low to high, making it ideal for the production of a wide variety of products that experience changes in viscosity.
Viscosity range
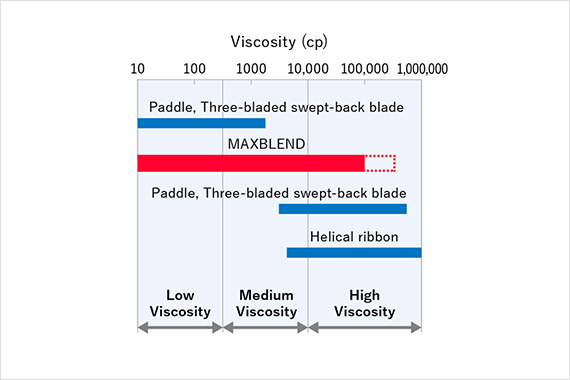
Mixture of different viscosity systems
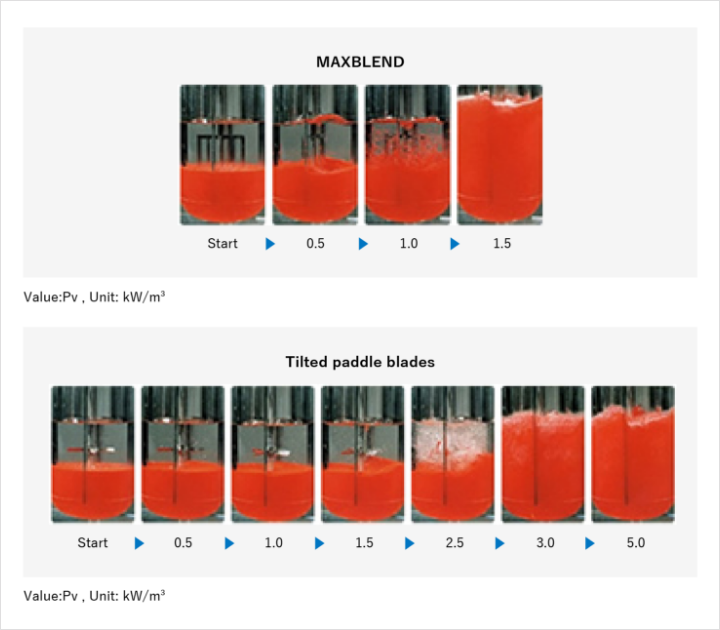
3. Stable to changes in liquid level
Conventional multi-stage blades had a problem of fluid circulation flow changing with the fluid level.
Maxblend has a continuous blade structure in the vertical direction, which provides stable performance against changes in liquid level.
(See mixing time comparison photo for a sample of the liquid circulation flow)
4. Excellent heat transfer characteristics
Higher heat transfer coefficients can be reached by the strong and uniform flow formed over the entire wall of the vessel. The synergistic effect with the high mixing performance results in a uniform temperature inside the vessel, and the small change in the liquid level lets the temperature control to be done with ease.
Comparison of heat transfer characteristics
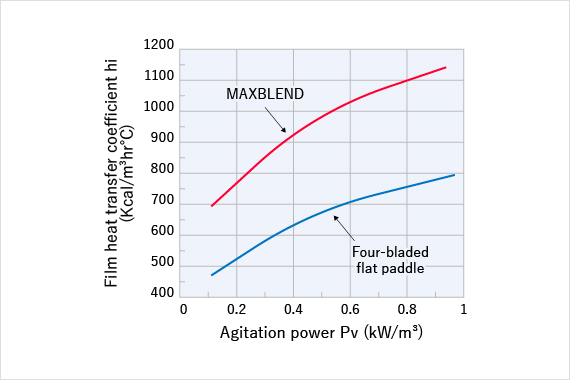
5. Low power consumption
Power consumption and heat source power consumption can be kept low by the low rotation and high mixing performance, which enables overall circulation to be efficient.
6. Uniform solid dispersion
Due to the strong discharge flow from the lower part of the vessel, uniform dispersion of solids can be achieved with low rotation and low power.
In addition, there is less local high shear area near the blade, which is seen in conventional blades, which minimizes physical breakage of solid particles.
Particle size distribution (MAXBLEND)
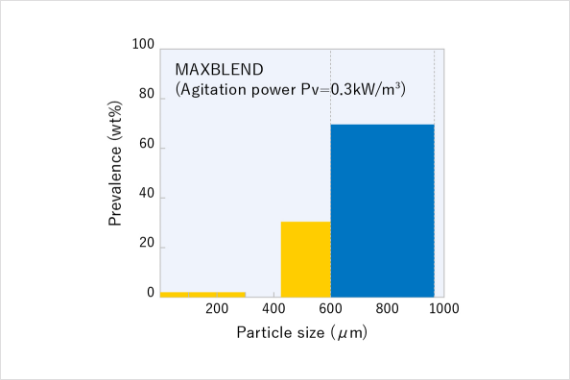
Particle size distribution (Flat paddle)
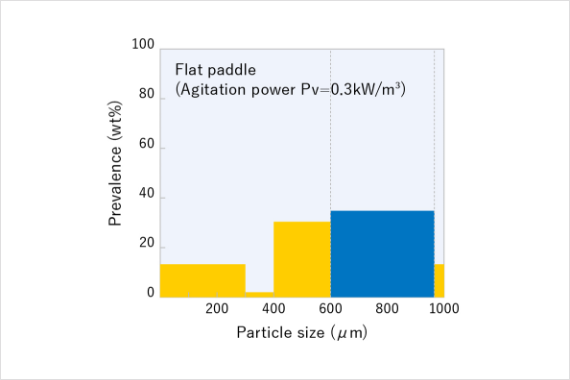
7. Easy particle size control
The uniform shearing effect ensures particle size distribution as sharp as shown below suspension polymerization and crystallization operations.
Variation by RPM (MAXBLEND)
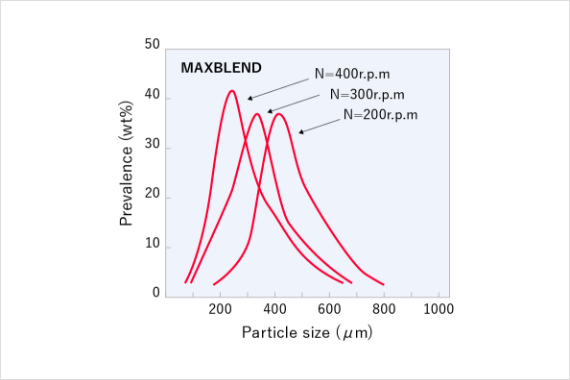
Variation by RPM (Flat paddle)
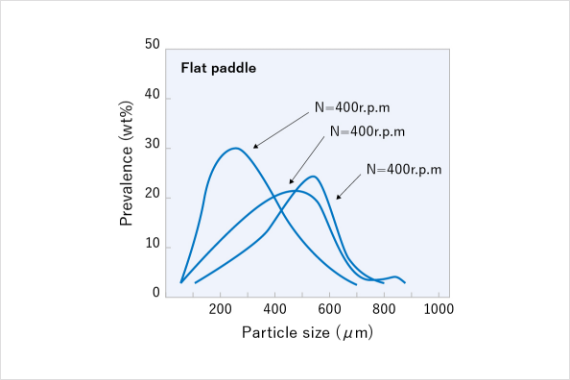
8. Minimum adhesion
The agitator eliminates the flow’s stagnant part and equalize the shearing force in the vessel . This results in uniform product properties and suppresses the generation of gelatinization and agglomeration, which greatly reduces the amount of adherence generated in various parts of the vessel.
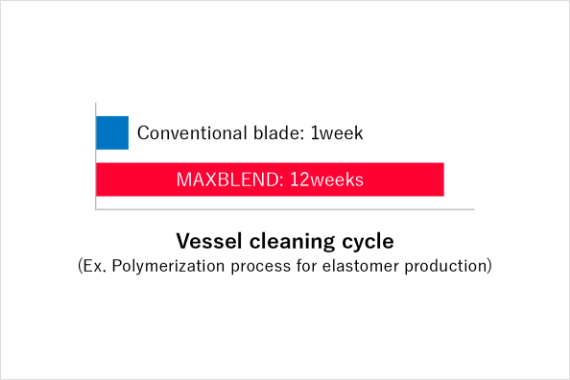
9. Excellent aeration and agitation characteristics
The gas dispersion in the vessel being high, excellent aeration performance can be expected even in a fermentation vessel that generally avoids high shear.
Comparison of agitation power
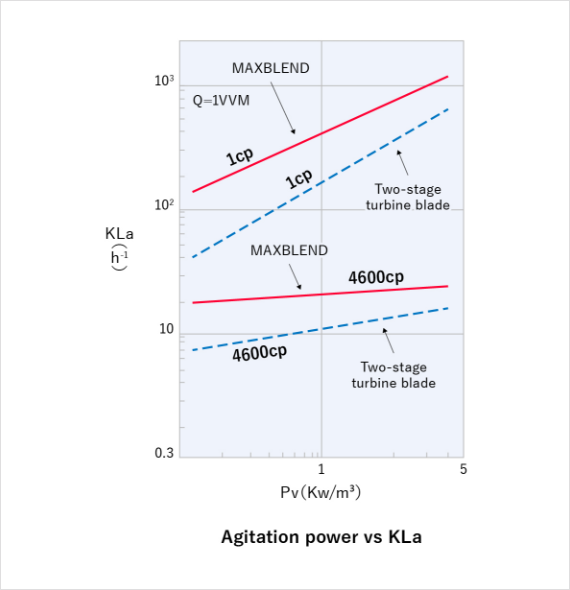
10. Glass lining for excellent corrosion resistance
Our highly anti corrosive standard GL, and the functional GL which maintains the same level of anti corrosion performance: NS-GL (Anti-electrostatic GL), NF-GL (low Na elution GL), and NEO-GL (high heat transfer GL) can be used for a wide range of acidic liquids.
* The glass-lined Maxblend agitation vessel was jointly developed by NGK Chemitech Ltd. and Sumitomo Heavy Industries Process Equipment Co.